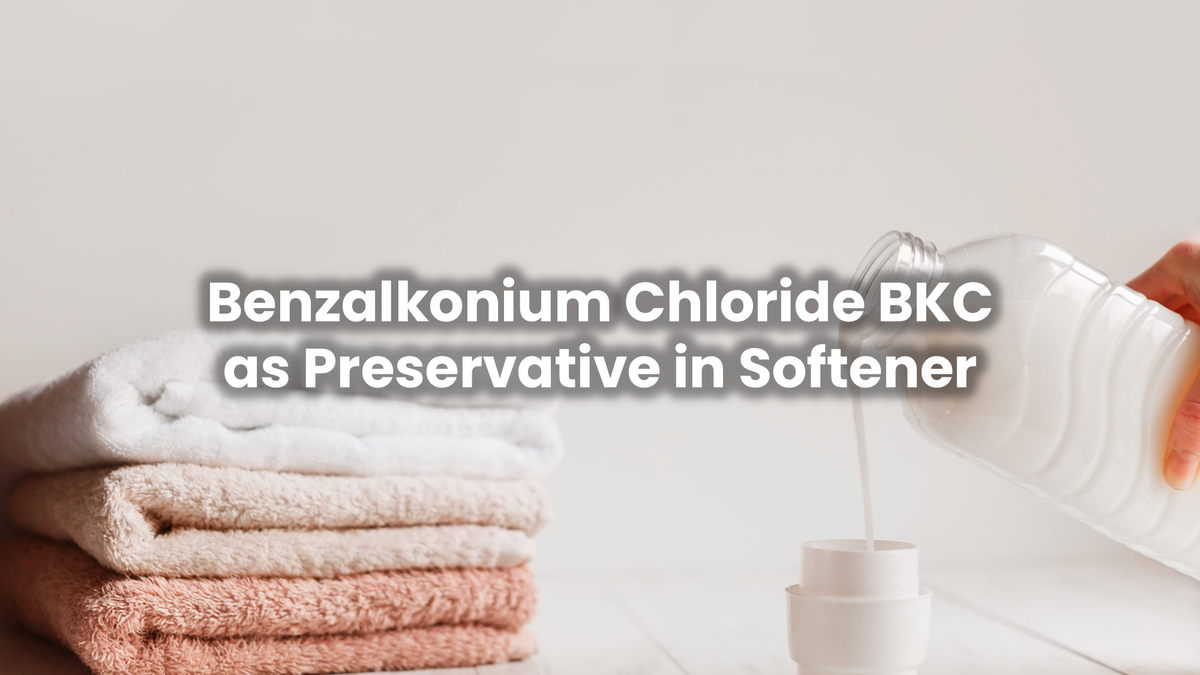
Fabric softeners are widely used in households and industries to improve the softness, fragrance, and static control of textiles. However, due to their water-based formulation, fabric softeners are highly susceptible to microbial contamination, which can lead to spoilage, foul odours, and reduced shelf life. To prevent this, Benzalkonium Chloride (BKC) is commonly used as a preservative in fabric softeners due to its effective antimicrobial properties. This article explores the role of BKC in fabric softeners, its benefits, proper usage, and other essential considerations.
What is Benzalkonium Chloride (BKC)?
Benzalkonium Chloride (BKC) is a quaternary ammonium compound (QAC) known for its broad-spectrum antimicrobial activity. It is widely used in disinfectants, sanitizers, personal care products, and industrial formulations. In fabric softeners, BKC functions primarily as a preservative, preventing bacterial and fungal growth that can degrade the product over time.
Why Fabric Softeners Need Preservatives?
Fabric softeners contain water and organic compounds that create an ideal environment for microbial growth. Without a preservative, the product can develop:
- Bacterial and fungal contamination: leading to spoilage and foul odours.
- Phase separation: reducing the effectiveness of the formulation.
- Loss of active ingredients: due to microbial degradation.
- Health risks: such as skin irritation caused by contaminated products.
BKC helps mitigate these risks by ensuring the stability and safety of fabric softeners during storage and usage.
Why is BKC Suitable for Use in Fabric Softeners?
One of the key reasons BKC is well-suited as a preservative in fabric softeners is its effectiveness in slightly acidic conditions. Fabric softeners typically have a pH range of 4.5 - 6.5, and BKC remains highly active in this range. Unlike some preservatives that degrade or lose efficacy in acidic environments, BKC retains its strong antimicrobial properties, making it an excellent choice for fabric softeners.
Additionally, BKC is highly compatible with the cationic surfactants found in fabric softeners. Many other preservatives may interact negatively with these surfactants, leading to instability or reduced effectiveness. BKC, however, integrates seamlessly into the formulation, ensuring long-lasting protection without affecting product performance.
How Does BKC Work as a Preservative?
BKC works by disrupting microbial cell membranes, leading to cell death. It is particularly effective against Gram-positive bacteria, Gram-negative bacteria, fungi, and algae. When used in fabric softeners, BKC remains active in both the liquid formulation and the diluted product during use, providing long-lasting protection.
Benefits of Using BKC in Fabric Softeners
- Broad-Spectrum Antimicrobial Action: Effective against bacteria, fungi, and algae.
- Non-Volatile and Stable: Ensures long-term preservation of the product.
- Compatible with Cationic Surfactants: Works well with fabric softener formulations.
- Prevents Odour Formation: Keeps the product fresh and free from microbial spoilage.
- Cost-Effective: Requires low concentrations for effective preservation.
- Effective in Slightly Acidic Conditions: Retains antimicrobial activity in fabric softeners' pH range.
- Safe for Consumer Use: At recommended levels, BKC does not pose risks to users.
Recommended Dosage of BKC in Fabric Softeners
The dosage of BKC in fabric softeners depends on various factors, including the formulation, storage conditions, and microbial challenge level. A general guideline is:
Application | Recommended BKC Concentration |
Household Fabric Softener | 0.05% - 0.2% |
Industrial Fabric Softener | 0.1% - 0.3% |
*Notes: The concentration should be optimized based on microbiological testing to ensure adequate preservation without affecting product performance.
How to Apply Benzalkonium Chloride (BKC) in Fabric Softener Formulation?
Step 1: Pre-Dissolution
- Dissolve BKC in water before adding it to the formulation to ensure uniform distribution.
Step 2: Addition to Fabric Softener Base
- Mix BKC with other ingredients under continuous stirring at 40-50°C to maintain stability.
Step 3: pH Adjustment
- Fabric softeners usually have a pH range of 4.5 - 6.5. Adjust pH if necessary, as extreme pH levels can reduce BKC’s efficacy.
Step 4: Homogenization and Quality Control
- Ensure the final product is well-mixed and undergoes microbial testing to confirm preservation effectiveness.
Factors Affecting BKC Efficacy in Fabric Softeners
Several factors influence the performance of BKC in fabric softeners:
- pH Level: BKC is most effective in slightly acidic to neutral pH.
- Compatibility with Other Ingredients: Avoid anionic surfactants that can reduce BKC’s antimicrobial activity.
- Water Hardness: High mineral content in water may reduce BKC’s effectiveness.
- Storage Conditions: Store fabric softeners in cool, dry places to maintain stability.
Safety and Regulatory Considerations
BKC is widely recognized as safe for use in personal care and household products when used within recommended limits. However, certain safety measures must be considered:
- Skin Sensitivity: Prolonged exposure to concentrated BKC may cause mild skin irritation.
- Environmental Impact: BKC is biodegradable but should be used responsibly to minimize environmental effects.
Alternatives to Benzalkonium Chloride in Fabric Softeners
While BKC is one of the most effective preservatives for fabric softeners, alternative preservatives include:
- Organic Acids (e.g., Sorbic Acid, Benzoic Acid): Milder but require lower pH for efficacy.
- Phenoxyethanol: Common in personal care but less effective against fungi.
These alternatives may be used alone or in combination with BKC for enhanced preservation.
Conclusion
Benzalkonium Chloride (BKC) is a highly effective preservative for fabric softeners, ensuring product stability, safety, and long shelf life. Its broad-spectrum antimicrobial properties, compatibility with cationic surfactants, and effectiveness in slightly acidic conditions make it an ideal choice for preserving fabric softener formulations. By using the correct dosage and formulation techniques, manufacturers can maintain high-quality products while preventing microbial contamination.